Enjoy the benefits of short drying time by applying FASTAR to an LPG Carrier
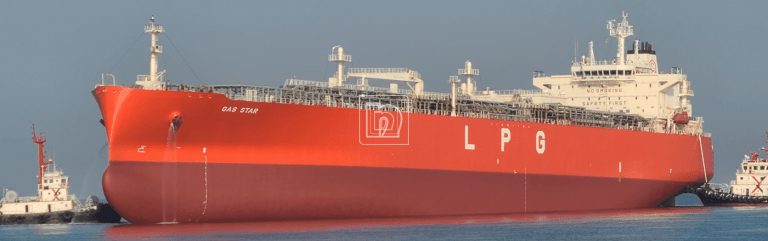
QUICK STATS
Vessel Owner | KSS LINE |
Vessel Name | M/T GAS STAR |
Location | Yeosu Ocean Shipyard., Korea |
Vessels | LPG Carrier / 78,000 CBM |
Type of Application | Drydocking |
Coating System | FASTAR I |
Application Vessel Area | Flat Bottom, Vertical Bottom and Boottop |
Date of Delivery | December 2021 |
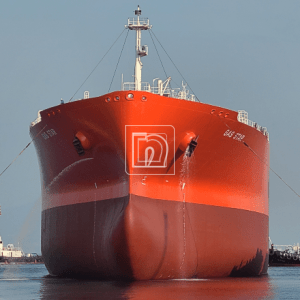
THE CASE STORY
In February this year, when South Korean ship operator KSS Line drydocked its 78,000m3 LPG carrier Gas Power at Sembcorp Marine’s Admiralty shipyard, the Nippon Paint Marine team in Singapore put forward a proposal to coat the hull with a system capable of reducing the vessel’s time in drydock while enhancing its operational efficiency.
The shipowner agreed that upgrading the 230m long ship’s existing A-LF Sea 150 antifouling to the new FASTAR I system was the best approach. The decision was an easy one to make given the success of an earlier upgrade to KSS Line’s 84,000m3 capacity Gas Star, which was applied in December 2021 at the Yeosu Ocean shipyard in Gwangyang Bay, South Korea.
In both cases, the FASTAR I coating was applied with relative simplicity to the vessels’ flat bottom and vertical sides, representing the first commercial reference for the new coating not only on a Korean-owned ship but also an LPG carrier.
While it is too early for the ships’ crew to verify the antifouling performance of FASTAR, what can be quickly confirmed is FASTAR’s short drying time which “was actually faster than we expected”. Indeed, this was a critical factor in a successful drydocking. The decision to apply FASTAR reduced application time by 37%.
KSS Line’s decision to move from the established A-LF-Sea range is indicative of the fuel saving quality of the low-polishing high-performing of the FASTAR antifouling system and other vessels in KSS Line’s 31 strong fleet are expected to adopt the new coating system at scheduled drydockings later this year.
With FASTAR, shipowners are benefitting from a tomorrow technology today.
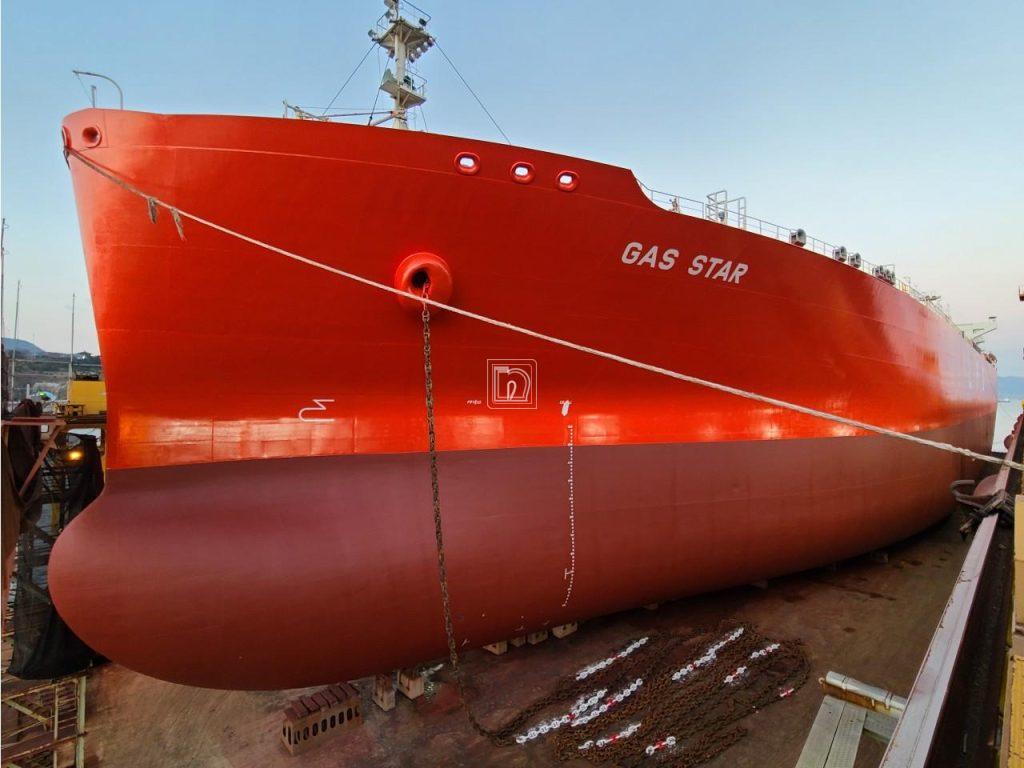